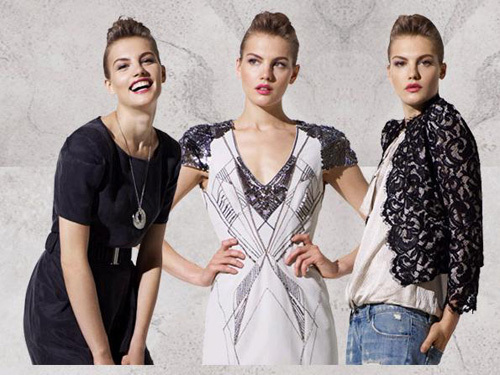
As the main battlefield for energy-saving emission reduction and elimination of backward production capacity, the printing and dyeing industry should be at the forefront. Whether it is the high pressure of national policies, the guidance of local governments, the guidance of industry associations, or the self-awakening of enterprises, in recent years, the printing and dyeing industry has made remarkable achievements in energy conservation and environmental protection, and sang the main theme of green development.
Environment pushes green awakening
According to environmental statistics in 2012, of the 41 industries surveyed and surveyed, textile wastewater discharges amounted to 2.37 billion tons, ranking third, chemical oxygen demand emissions 277,000 tons, ranking fourth, ammonia nitrogen emissions 1.9 Ten thousand tons, ranking fourth. Of the 972 nationally controlled sections monitored by the ten major river systems, the proportions of Grade I-III, IV-V, and inferior-V water quality sections were 63.1%, 25.3%, and 11.6%, respectively. The main pollution indicators were chemical oxygen demand, BOD5 and total phosphorus, and the total number of IV-V and inferior V sections in the Liaohe, Huaihe and Haihe river systems exceeded 50%. Especially in the eastern part where the economy is developing rapidly, the pollution is the heaviest. Strengthening environmental governance has reached a point of no time.
“Now the national access to printing and dyeing policy is becoming more and more stringent. Indirect wastewater discharge standards have been raised to CODCr 200mg/L, sensitive areas have even reached CODCr 60mg/L; the country has not included dyeing and printing sludge in the hazardous waste list, but in the environmental management process In the meantime, the printing and dyeing sludge is treated as hazardous waste; exhaust gas, sludge, and elimination of backwardness are thresholds everywhere, and enterprises will not be eliminated sooner or later if they do not increase input.†An owner of a printing and dyeing company in Shaoxing introduced this year’s Shaoxing area. More than 90 printing and dyeing enterprises through the form of mortgage of waste water discharge rights, from the bank 1.66 billion yuan for environmental protection.
From the National Catalogue of Hazardous Wastes, the Discharge Standards for Water Pollutants in the Textile Dyeing and Finishing Industry, and the Guidelines for Environmental Abiding Laws of Printing and Dyeing Enterprises, the pressure of the environment has forced the transformation and upgrading of the industry step by step, and the printing and dyeing industry has been reshuffled. “Actually, at present, the level of energy saving, emission reduction and environmental protection in China is not low in the world, including emission standards that are higher than those in Europe and the United States. Why is the impact on the environment still relatively large? The main reason is that our industrial concentration is very high. A small area has gathered a large number of companies. Due to cumulative effects, the impact on the environment is relatively large.†Chen Zhihua, president of the China Printing and Dyeing Association, said that since the textile dyeing and finishing industry is a large water user and a major sewage emitter, it is currently developing in many places. Are subject to restrictions.
In order to promote advanced environmental protection technologies and experience and accelerate the pace of energy conservation and environmental protection in the industry, the China Printing and Dyeing Industry Association has organized the “National Energy Saving and Environmental Protection Annual Conference of Printing and Dyeing Industry†since 2006. “Every time we hold an environmental conference, we exchange and push the factory for some key common technologies encountered in the process of energy conservation and emission reduction that are common in the production process of the industry.†Chen Zhihua said that in recent years, the entire printing and dyeing industry The technological level and product level have been greatly improved, the proportion of advanced equipment in the industry has been continuously improved, and energy-saving and emission-reduction, clean production, and ecological security are steadily advancing.
Science and technology help innovation and development
In the product exhibition of Zhejiang Shengfa Textile Printing and Dyeing Co., Ltd., a special ** fabric was placed in a prominent position, attracting the attention of visitors, this is the "nano-functional ** fabric." “Compared to ordinary fabrics, the fabrics are characterized by high strength, strong corrosion resistance and good air permeability, and are widely used in military apparel and equipment manufacturing.†Yang Wenlong, chairman of Shengfa Textile, said that only this fabric can be used for one year. Brought a production value of 100 million yuan to Shengfa Textile, accounting for 1/4 of the company's annual production value. In order to innovate, Shengfa Textile does not hesitate to invest, invest 150 million yuan to introduce advanced equipment and technical personnel, develop new fabrics and printing and dyeing technologies; look for expert experts in three fields, and Shanghai Donghua University, Xi’an University of Engineering, etc., have strength, research and development capabilities Universities and scientific research institutes have established cooperation between production, education and research. The establishment of a laboratory that is comparable to the national standard, the Academician of Zhejiang Shengfa Textile Printing and Dyeing Co., Ltd., has injected vitality into the company's scientific and technological innovation. "For enterprises, establishing academicians' workstations is a deterrent to transformation and upgrading." In Yang Wenlong's view, "Innovation is to solve today's problems; creation is for tomorrow's goals."
Like Yang Wenlong, many printing and dyeing companies have actively invested in this "green battle." Because they firmly believe that only the power of science and technology can change the future of the company and save the development of the industry. “The textile industry is now at an extremely difficult time of development, not only being squeezed by the original textile giants, but also facing the competition of emerging countries in economic development. With the continuous tightening of national environmental protection policies, printing and dyeing companies must rely on production. Studying and researching cooperation will break new ground for technological innovation."
Yao Mu, an academician of the Chinese Academy of Engineering, pointed out that the sustainable development of the printing and dyeing industry must adhere to the two-fold approach of “innovation-driven, quality first, green development, structural optimization, and integration of the twoâ€.
Please look directly into the printing and dyeing
Many people will still have a look at the suspension of production of all printing and dyeing plants and water jet loom factories in this year's Wujiang area. Because the local environmental protection department detected excessive levels of niobium in drinking water sources in the Taipu River at the junction of Jiangsu, Zhejiang and Shanghai, and then adopted “decisive†behavior, the entire industry became panicked. To this end, Professor Tan Dayli of Donghua University pointed out when publishing the “Countermeasures and Reflections on Pollution in the Printing and Dyeing Industry†that the source of germanium in the textile printing and dyeing industry is mainly the synthesis of polyester (polyester raw material): when terephthalic acid and ethylene glycol are synthesized 300-500ppm of antimony trioxide, antimony acetate or ethyleneglycol antimony were used as catalysts; the flame retardant in dyeing and finishing had almost no antimony compound three years ago, and there were almost no dyes and additives. The local government's practice on printing and dyeing enterprises was very practical. It is difficult to "differ." At the same time, Dan Li-li also announced that printing and dyeing companies measured: 锑100~500μg/L, very few more than 1000μg/L; water-jet loom factory is about 30~100μg/L (this is the case in 1/4 companies) Sewage treatment plant 210μg/L, effluent 80μg/L. “I hope the relevant departments and organizations will promptly identify ** and give a fair answer to the printing and dyeing industry. Prior to this incident, it was the nonylphenol incident. Now that it has become polluted, what happens after the pollution occurs?
Although there is still a certain gap between the current consumption and energy consumption of the best technology and equipment in the printing and dyeing industry in China, it cannot deny the achievements of the printing and dyeing industry in recent years. Sun Ruizhe, vice president of the China Textile Industry Federation, pointed out during the "12th Five-Year Plan" midterm evaluation report for China's textile industry that the comprehensive energy consumption of textile enterprises above the designated size in 2012 was 61.74 million tons of standard coal, which was 4.2% lower than that in 2010, and the number of units increased. The values ​​of energy consumption and CO2 emission intensity have fallen by 25% compared with 2010, and the “planning†target has been completed; some indicators of emission reduction cannot be continuously compared due to statistical adjustments. It is estimated that the value added of textile industry units in 2011 is higher than that of 2010. It has dropped by 29.8% year-on-year and has also basically completed the "planning" goal.
“In fact, the printing and dyeing industry still has a lot of potential to tap in terms of technology, equipment, and management, especially in accelerating the adjustment of industrial structure and product mix. If we increase the proportion of knitted products, it will help reduce the overall energy consumption. It is estimated that the energy saving per unit product will increase by 8%~12%, while the overall energy saving rate of all products will increase by 2%~6%, and the gradual improvement and promotion of new technologies and new processes, such as the promotion of cold rolling and pushing technology, can save energy. 30%.†Dan Li-li stated that if the transformation investment is calculated at RMB 42.52 billion annually from 2011 to 2015, the conversion investment from 2016 to 2020 will be calculated at 35.64 billion yuan, of which the increase in profits will increase the investment by RMB 30 billion annually. Around yuan, the textile industry itself will be difficult to digest, and the state needs to give considerable incentives, in particular, a certain percentage of income tax, business tax, and technical support for financial support.
Nowadays, whether it is a printing and dyeing enterprise or a printing and dyeing cluster, Shaoxing and Shishi have all increased the intensity and speed of environmental protection, making green printing and dyeing a common practice. The environmental protection issue is not a problem that can be solved and realized by a company and an industry. Therefore, it is necessary to unite, integrate resources, and integrate strength in order to achieve a sustainable and healthy development of the industry.
- Polyester Fabric has high strength and elastic recovery. Therefore, it`s firm and durable, wrinkle-free iron.
- Polyester fabric is easy to dry after washing, and the wet strength almost does not decrease.
- Polyester fabric has better light-resistance than natural fiber fabric.
- Polyester fabric has good resistance to various chemicals. ACID, Alkali on its damage are not big, and it is not afraid of mold or moth.
Strip Polyester Fabric,Polyester Spandex Fabric,Polyester Blend Fabric,Black And White Striped Fabric
Shaoxing Haitang Textile Co., Ltd. , https://www.haitangfabric.com